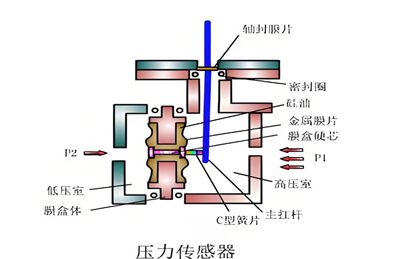
Working principle of pressure sensor
Pressure sensors are sensors that convert pressure into electrical signals for output. Different types of pressure sensors have different working principles. Here are some common working principles of pressure sensors:
-* * Piezoresistive pressure sensor * *:
-Working principle: When pressure is applied to the diaphragm of the sensor, the diaphragm undergoes deformation, causing a change in the resistance value of the strain resistor attached to the diaphragm (this phenomenon is called the resistance strain effect). Usually, strain resistors are used to form a Wheatstone bridge, and membrane deformation can cause the bridge to lose balance, resulting in the output of a voltage signal related to pressure changes.
-Application scenarios: Widely used in various industrial automation environments, such as water conservancy and hydropower, railway transportation, intelligent buildings, etc., it can be used to measure the pressure of gases or liquids.
-* * Piezoelectric pressure sensor * *:
-Working principle: Based on the piezoelectric effect, certain piezoelectric materials (such as quartz crystals, ceramics, etc.) will generate charges when subjected to pressure, and the generated charges are proportional to the change in pressure. However, piezoelectric sensors cannot be used for static measurements because the charge generated by external forces can only be preserved when the circuit has an infinite input impedance, which is not the case in reality. Therefore, they are only suitable for dynamic measurements.
-Application scenarios: Commonly used for measuring acceleration, pressure, and force, such as vibration and impact measurement in aircraft, automobiles, ships, etc. It can also be used to measure internal combustion pressure of engines, changes in bullet chamber pressure, etc.
-* * Capacitive pressure sensor * *:
-Working principle: Using capacitors as sensitive components, the measured pressure is converted into changes in the capacitance value. Usually, a circular metal film or a metal coated film is used as one electrode of a capacitor. When the film deforms under pressure, the capacitance between the film and the fixed electrode changes, and an electrical signal related to the voltage can be output through a measurement circuit. Capacitive pressure sensors can be divided into single capacitor and differential capacitor types. Differential capacitor type has higher sensitivity and better linearity, but it is difficult to process and cannot achieve isolation of the measured gas or liquid. Therefore, it is not suitable to work in fluids with corrosiveness or impurities.
-Application scenario: Suitable for measuring small pressure changes, such as in some high-precision pressure measuring instruments.
-* * Strain gauge pressure sensor * *:
-Working principle: It includes a sensing element (diaphragm). When the diaphragm is deformed under pressure, it will cause a change in the resistance of the strain gauge attached to the diaphragm. The Wheatstone bridge circuit is usually used to convert resistance changes into usable output signals to reflect the magnitude of applied pressure.
-Application scenarios: Suitable for measuring extremely high and low pressures and pressure differentials, with applications in industrial production, aerospace and other fields.
-Potential pressure sensor:
-Working principle: Composed of a precision potentiometer, the wiper blade of the potentiometer is connected to a pressure sensitive element (such as a diaphragm). The pressure causes the diaphragm to deflect, thereby changing the position of the wiper blade and causing a change in the resistance value between the cursor and one end of the potentiometer. This change in resistance value reflects the magnitude of the applied pressure.
-Application scenario: It can be used in situations where pressure measurement accuracy is not particularly high.
-* * Resonant line pressure sensor * *:
-Working principle: Its core component is the vibrating wire located in the diaphragm. The electronic oscillator keeps the metal wire vibrating. When the pressure in the diaphragm changes, it affects the tension of the metal wire and changes the resonance frequency. This frequency change can be sensed by a digital counter circuit and converted into an electrical signal to represent the magnitude of the pressure.
-Application scenario: Suitable for situations with high requirements for pressure measurement accuracy and special working environments, such as high temperature, high pressure, etc.
-Inductive pressure sensor:
-Working principle: Using the principle of electromagnetic induction, the transducer of the sensor has a diaphragm connected to the ferromagnetic core. The slight deflection of the diaphragm will cause linear motion of the ferromagnetic core, thereby inducing current in the coil. Due to the movement of the magnetic core caused by pressure changes, the induced current will change. Converting this current change into a usable signal can reflect the change in pressure.
-Application scenarios: commonly used in situations that require non-contact pressure measurement, or in environments that require high reliability and stability of the measurement.
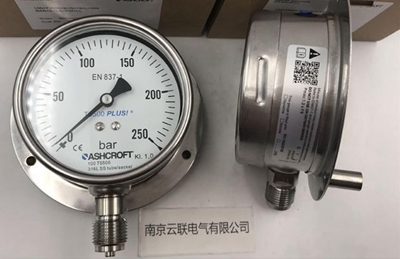